Le frittage sélectif par laser (SLS)
- 17 août 2017
- 3 min de lecture

Pour mieux vous faire comprendre les principales techniques d’impression 3D que nous utilisons, nous avons décidé de faire des news sur chacune d’entre elles. Aujourd’hui nous faisons un focus sur la technique du frittage sélectif par laser (SLS).
Le procédé de frittage sélectif par laser ou selective laser sintering (SLS) en anglais a été développé par Carl Deckard, un inventeur, enseignant et businessman à l’Université du Texas à Austin, dans le milieu des années 1980. Ce procédé fut ensuite brevetée par DTM Corporation, racheté par la suite par l'entreprise 3D Systems.
Cette technique consiste à fabriquer une pièce couche par couche avec de la poudre par frittage laser. En d’autres termes, cette technique utilise des matériaux sous forme de poudre qui sont ensuite chauffés et assemblés couche par couche grâce à un laser pour former la pièce souhaitée.
Le procédé est simple : Comme pour tout projet réalisé par fabrication additive, tout commence par la conception de l’objet à partir d’un logiciel de CAO. Puis, placée dans un bac réservoir, la poudre est déposée par couche fine (de l’ordre de 0,1 mm) dans un autre bac initialement vide à l’aide d’un rouleau. La couche déposée est ensuite balayée par un puissant faisceau laser qui suit le tracé de la pièce et va fusionner puis consolider la poudre. Le bac d'impression descend ensuite légèrement (de l'épaisseur d'une couche). Les étapes précédentes sont ainsi répétées jusqu’à obtention de la pièce voulu.
Pour vous aider à mieux comprendre, voici une vidéo schématisant le procédé :
Après impression, vient la phase de dépoudrage car la pièce se retrouve noyée parmi un bloc de poudre. Il faut donc, à l'aide d'une brosse, retirer le plus gros de la poudre puis avec une soufflette, enlever ce qu'il reste de poudre dans une machine prévue à cet effet.
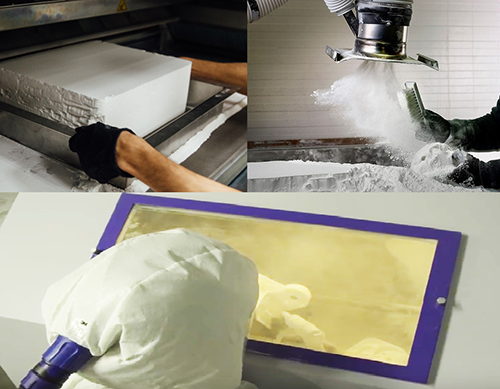
L’avantage de cette technique est qu’elle permet d’imprimer des pièces fonctionnelles, très solides et d’une finesse exceptionnelle sans avoir recours à une éventuelle étape d’assemblage. Et contrairement à d’autres méthodes d’impression, elle ne nécessite pas de support puisque la poudre agit elle-même en tant que tel. Néanmoins, il n’est possible d’imprimer qu’en une seule couleur, mais nous en proposons une large palette.
Les matériaux utilisés sont divers et variés (Métaux, nylon, alumide, etc…). Par conséquent, cette technique répond à un très grand nombre de besoins et est non seulement utilisée dans l’industrie du design mais également dans l’automobile ou l’aéronautique par exemple.
Voici quelques exemples de réalisations :

Toutes ces pièces ont été réalisées en PA 2000 (nylon)
> La première pièce est un prototype pour protection de guidons de motos. Une mousse vient se mettre par-dessus pour éviter de se taper la tête. Le but était d’optimiser la pièce que notre client produisait à l’origine par réduction du poids et de la matière. Une fois le prototype testé et validé, notre client a pu faire fabriquer un nouveau moule pour injection en grande série.
> La deuxième est une pièce de démonstration, réalisable uniquement par Impression 3D, les techniques d’usinages traditionnelles ne pouvant produire une telle pièce dû à la complexité de l’intérieur du dé.
> La troisième pièce est un outil de montage et de centrage d’une jupe de pare-choc de camion pour un de nos client, célèbre et réputé fabricant de camion. Voici un lien pour découvrir plus en détails ce projet.
> La quatrième est un trophée en alumide avec de la poudre chargée en paillette d’aluminium.
> La cinquième est une pièce de rechange pour un particulier (siphon de douche).
> La dernière est une pièce faisant parti d’un système d’engrenage, réalisé en 10 exemplaires pour un inventeur.
Voici un autre exemple avec une pièce de rechange avant/après :

Il s'agit d'une pièce de manivelle pour l'ouverture du toit d'un camping car.
Nous utilisons beaucoup cette technique, notamment avec l’imprimante « EOS FORMIGA P110 » dont vous pouvez voir un exemple sur la vidéo suivante :
Les imprimantes utilisant cette technique deviennent de plus en plus accessibles.
Disruptive, l'imprimante 3D "Sinterit Lisa" sera notre prochaine acquisition. En plus de son design innovant, sa haute qualité d'impression et sa petite taille, cette imprimante SLS est accessible à petit prix !
Après en avoir testé toutes les possibilités, nous la proposerons à la vente afin de permettre à nos clients de goûter aux joies du SLS !
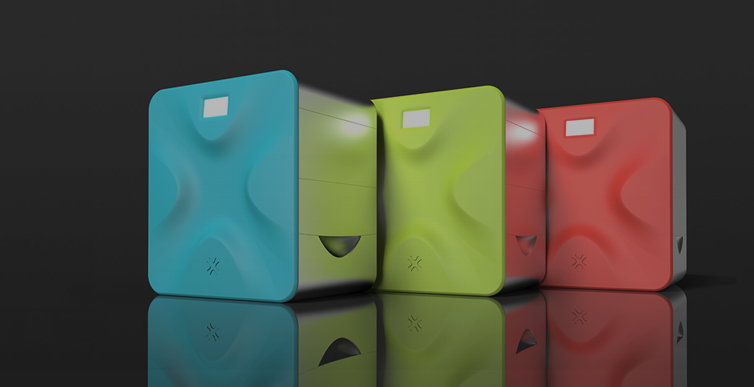
Source : https://3dprintingindustry.com/
Komentar